Manufacturing Zero Water Peak Single-Mode Fiber
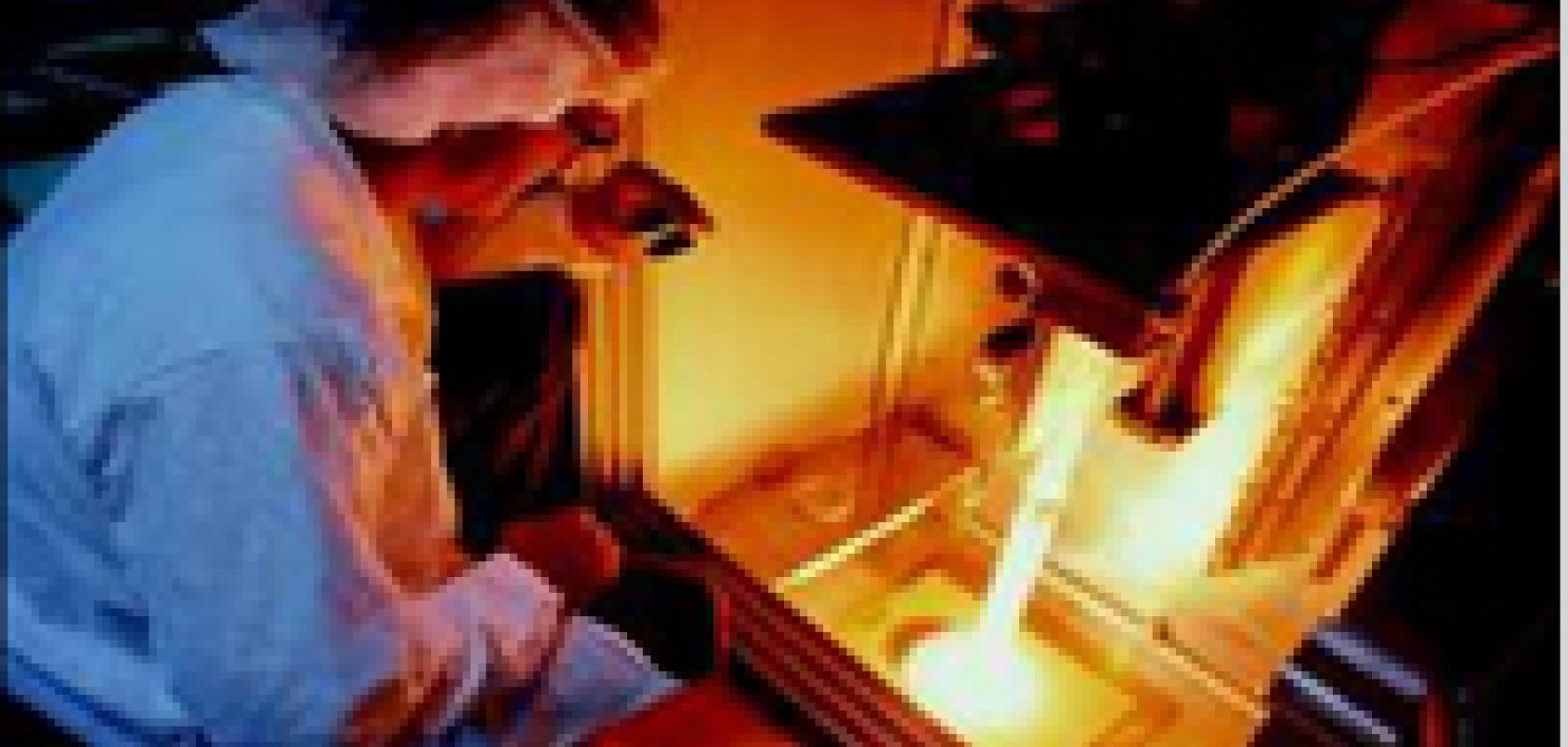
OFS single-mode optical fiber helps end users meet the growing demand for voice, data, and video transmission at ever-faster speeds.
Generally designed for systems of moderate to long distances (e.g., metro, access, and long-haul net- works), our single-mode products include AllWave® fiber, the industrys first zero water peak (ZWP) fiber, and bend-optimized products like AllWave FLEX+ Fiber. These products seamlessly extend the optical network into the end userís premises with outstanding reliabil- ity and very low loss.
Single-mode fibers have a small core size (< 10 µm) that permits only one mode or ray of light to be transmitted. This tiny core requires precision alignment to inject light from the transceiver into the core. The core is surrounded by another glass layer called the cladding, a 125-µm region that confines the light signal within its path. Manu- facturing single-mode optical fiber is a highly controlled process requiring maintenance of extremely tight tolerances.
Manufacturing the Preform
OFS manufactures its AllWave fiber cores using a patented vapor axial deposition (VAD) process, which takes place in an ultra-clean environment. The process begins with a 'target' rod made of high- quality quartz glass. Gaseous raw materials are sprayed in the presence of a flame. The resulting chemical reactions generate a porous white soot that is deposited on the target rod.
The process uses two torches. The first torch forms a Germania-doped silica soot and deposits it in the center to form the core or "waveguide" region, in which light is transmitted. The second torch deposits ultra-pure silica soot on the outside of the core region to ensure the fiber has low loss. The rotating target rod is slowly pulled away from the torches, leaving a large porous core rod.
Next, the porous core rod is de-hydrated and purified. The rod is placed in a furnace at ~1200°C, where chlorine gas is added to purify the glass, removing excess OH ions and leaving purified silica with germanium dopants. This step enables OFS to offer ZWP glass for each of its AllWave fiber types, with low attenuation throughout the entire optical spectrum.
The furnace temperature is then increased to ~1500°C and helium is added to transform the porous glass matrix into a clear, void-free glass. Within the furnace, surface tension pulls the high surface area soot into a solid glass core rod.
At this point, the diameter of the core is optimized in a process called elongation. Here, the core rod is scanned for dimensionality, heated, and pulled to generate a uniform target diameter throughout its entire length. A second scan is conducted to ensure that the waveguide is the desired size and completely symmetrical.
The elongation process puts a small amount of additional hydrogen in the core rod surface. This layer of OH on the core rod surface must be removed in a process called etching, in which the pre-form is sprayed with hydrofluoric acid (one of few materials that can dissolve glass).
Once completed, several VAD core rods which have been precisely matched to ensure uniform properties in the resulting fiber are inserted into a long synthetic quartz cylinder that forms the bulk of the cladding region for the optical fiber. This glass assembly is fused together to form a fully collapsed preform that is the basis for thousands of kilometers of fiber.
Fiber Draw
The preform assembly is conveyed to the top of a tall tower, where it is lowered into a furnace that melts the glass tip. Then, gravity takes over, as the glass drops in a thin strand to the bottom of the tower, where it is reeled onto a take-up spool. Precise control of the furnace temperature and pulling conditions help to ensure the fiber meets the demanding specifications of the resulting optical fiber.
All along the fiber's path, gauges are used to measure and control geometric properties such as the fiber's diameter, which is controlled to 125 ± 0.7 µm. This level of control improves the connectorization process and also helps to ensure proper coupling of the light source to the fiberís core.
During the draw process, acrylate coating is applied and cured in a series of UV ovens. All OFS single- mode fibers feature our D-LUX® Coating, which protects the pristine silica fiber from the environment and promotes long-term reliability. Gauges within the tower continuously monitor key parameters such as clad diameter, coating diameter, and clad-coating concentricity. In this state-of-the-art draw process, the finished fiber has the same index profile as the preform from which it is drawn.
To protect against polarization mode dispersion (PMD), which could otherwise limit distances and data rates in a single-mode optical fiber system, a patented OFS technology creates a "spin" within the fiber during the draw process to reduce birefringence. In this process, an oscillating sheave imparts spin to the fiber at the base of the draw tower.
The spin then propagates upward to the neck-down region where the molten glass is spun first one way and then the other. As the glass cools, the spin is "locked in" to the fiber. The angle of the spin and the rate of oscillation can be varied to impart different end-use characteristics.
Quality Control
At OFS, each spool of fiber is measured to validate that the product will meet stringent industry and internal specifications. These tests measure geometric properties such as clad diameter and circularity and optical properties such as attenuation, dispersion, and cut-off wavelength. Fiber proof-testing to 100 kpsi helps ensure long-term reliability for every single-mode fiber we produce.
Our industry-leading AllWave Zero Water Peak Fiber virtually eliminates the high loss known as a "water peak" caused by water absorption in the 1360 - 1460 nm band. To enable us to manufacture ZWP fiber, the drawn fiber receives a treatment of deuterium (D or 2H, also known as heavy hydrogen). Deuterium, one of two stable isotopes of hydrogen, fills any voids in the molecular structure of the glass, making it difficult for regular hydrogen to react with the glass structure, thereby virtually eliminating the absorption peak.
Summary
Fabricating high-performance fibers requires innovative designs and processes. A stable, accurate manufacturing process, such as OFS' VAD method, is essential to produce these products in significant quantities. Measurement data must be fed back to the process on a real-time basis to ensure consistently high fiber performance.
A leading-edge fiber draw process must be used to optimize fiber performance and precisely control dimensions. Sophisticated process control tuning methods are required to adjust manufacturing conditions to create and maintain precise fiber profiles.
Together, these manufacturing and testing processes can produce high-performance zero water peak single-mode fibers that provide customers with cost-effective solutions for today's networks.
For additional information contact your sales representative. You can also visit our website at www.ofsoptics.com or call 1-88-fiberhelp.
Copyright © 2013 OFS FITEL, LLC All rights reserved
A Furukawa Company