The recent Covid-19 pandemic has changed many areas of our daily life, from going to a place of work, how we spend our holidays, to eating out and socialising with friends and family. For fibre engineers, it has arguably had a much greater impact.
When lockdown was announced in March, while many were able work at home, those in industries deemed ‘key workers’ carried on. For example, in the UK, government guidance as to which roles were included, referenced the ‘information technology and data infrastructure sector and primary industry supplies to continue during the Covid-19 response; and key staff working in the civil nuclear, chemicals and telecommunications sectors (including, but not limited to, network operations, field engineering, call centre staff, IT and data infrastructure, 999 and 111 critical services).’
Time critical
We’ve all read accounts of engineers being insulted and threatened in the street by people who believe that Covid-19 is somehow linked to 5G, and that the fibre engineers are somehow installing 5G in the ground! It stands to reason that engineers need to be as efficient as possible, so no more time is spent on a job than absolutely necessary. Of course, it is not just to avoid conspiracy theorists. If an engineer is undertaking work in a busy area – or in someone’s home – they will want to limit the time there in order to best minimise any potential risk.
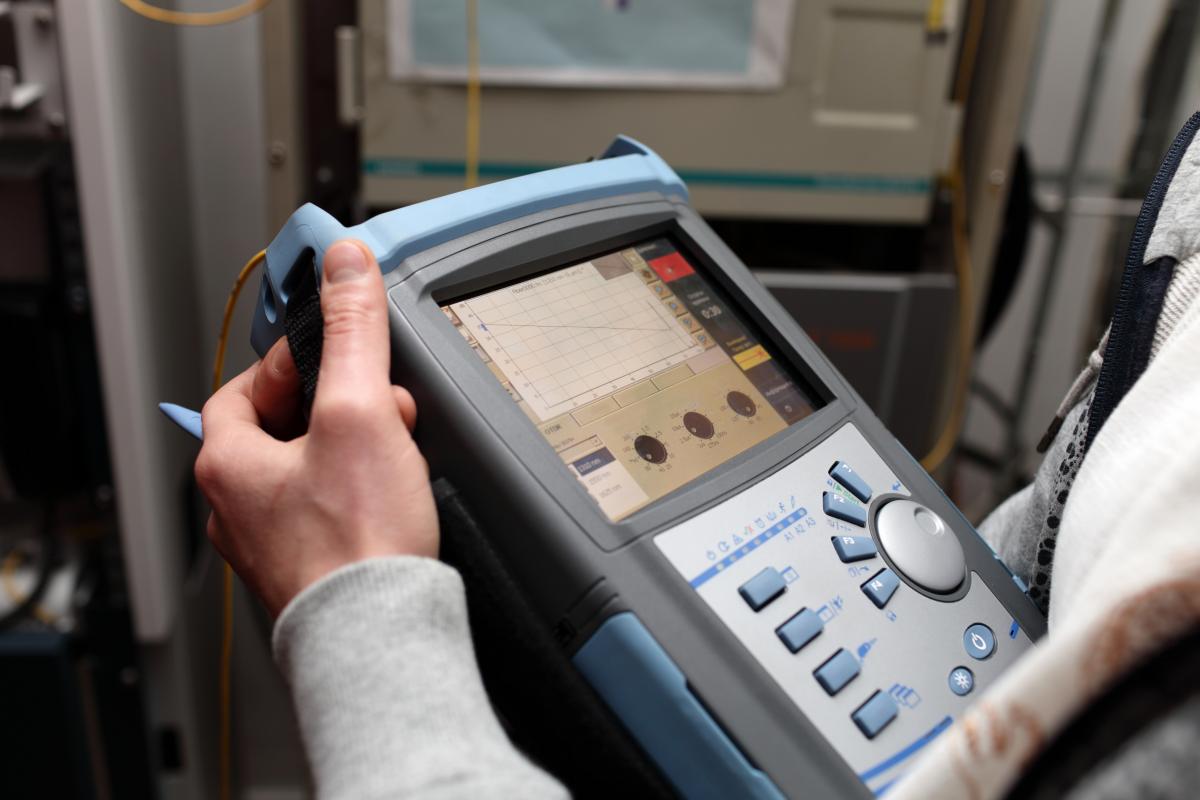
Koji Okamoto, VP/GM, fibre and access business at Viavi Solutions explained: ‘Even as lockdowns have eased, communication service providers still need to keep front-line technicians safe by limiting their time in the field – while adhering to social distancing guidelines. At the same time, service activation and operation are becoming ever more complex, as next-generation networks span many diverse technologies and legacy systems.’
Okamoto said that to address these converging challenges, fibre network operators are looking for ways to make field operations faster and more efficient, allowing front-line technicians to reduce time in the field, even as they deploy, maintain and optimise networks.
’By improving test process efficiency, field technicians can more easily address issues such as components that are defective or damaged during installation, pressure to meet daily quotas leading to human error, and exceedingly complex deployment processes that are difficult and time-consuming, leading to faster deployment and more effective troubleshooting,’ he said.
Shock absorber
Douglas Clague, solutions marketing manager at Viavi, agreed, and raised another important aspect of any tool that is used in a wide range of terrains. ‘When we design these things we always have the users in mind. From the hardware, the software, it’s about how people interact with it. As far as the hardware goes, for installers in the field, it has to be rugged, so vendors have to put time and effort into making sure equipment is as ruggedised as possible. That’s both internally and externally. It’s not a question of just putting some rubber bumpers onto it, we have to look at – in the case of spectrum analysers, for example – the hardware we use to make our measurements and we always adopt material that can withstand shock.’
Matt Tyrk, technical sales engineer at Laser Components, concurs. ‘On-site equipment needs to be precise, but also water and dust-resistant,’ he said.
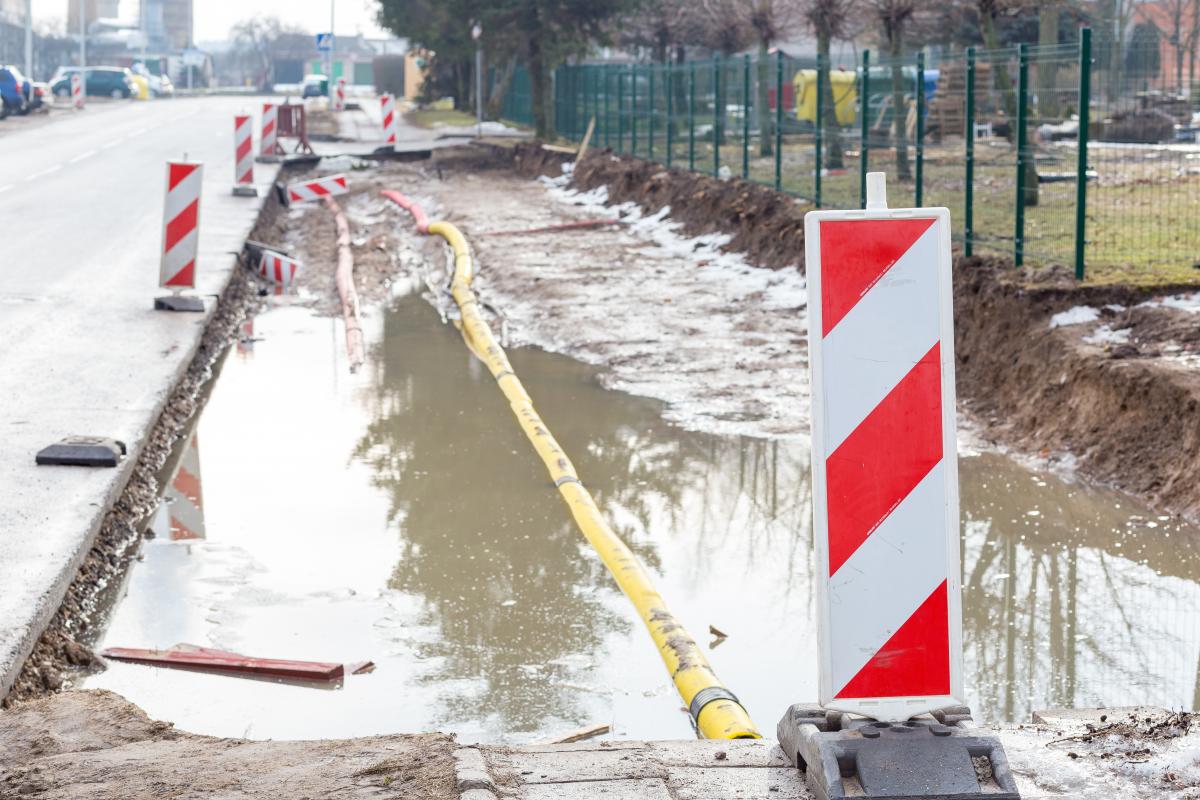
‘OTDRs are mostly used for fault locations, so need to be nice and small and simple to use in the field, with very tight dynamic range that allows for longer cables. Importantly, they must also be impact-resistant – you never know what’s going to happen in the field, it’s not like it’s a lab environment.’
This is particularly important when you consider that many engineers and installers are contractors, and have to outlay for their own equipment. A broken piece of kit could be the difference between a paid job or lack thereof.
Efficiency is also a critical factor for contracting engineers, so that they are able to schedule more jobs. Clague elaborated: ‘The techs out in the field are under time pressure, they’re always under the gun, so equipment has to be easy to work with. When they get to site it has to switch on quickly, then it has to be quick to set up and then easy to use, and when they’re finished testing it has to be easy to interpret the result.’
Time is money
As an example, engineers delivering with high-fibre-count cables need to not only run the tests – and the more fibres, the more testing – but also store the results, naming each file and saving each time. This is no mean feat and can add huge amounts of time to a job. Vendors need to look at how to streamline these processes.
‘We actually go a bit further than that now,’ explained Clague. ‘We’ve added what we call assistant apps, and they can bring the set-up and configuration of OTDRs down to just a couple of screen clicks.’
‘Mobile applications are an important part of today’s testing processes,’ added Okamoto. ‘They allow techs to multi-task and remotely control test instruments. This is especially important for techs who are running several tests concurrently, or those who are working in inclement conditions. Such apps enable techs to attach the instrument to the network and remotely control it from a mobile device, thereby limiting time spent in the field.’
Another group to benefit from designed-in-simplicity is the newer techs and apprentices, or those who have migrated from a copper or coax environment. ‘Getting trained and becoming effective is an issue,’ said Clague. ‘There is a learning curve there. The simpler the kit is to set up, the more interpretation of results that we do, the better. We take the OTDR trace and turn it into something easier to digest. Anything we, as vendors, can do to soften that curve is a good thing.’
As is so often the case, another key consideration for engineers is cost. Tyrk elaborated: ‘We always try to choose products that are cost-effective. Engineers tell us that this is the most important thing. If you’ve got a dense wavelength division multiplexing (DWDM) or a coarse wavelength division multiplexing (CWDM) network, for example, it’s full of different wavelengths and you need to measure each signal of those wavelengths. You would typically need a DWCM or CWDM power meter. Often, technicians won’t use them because they are very expensive, so we made a device that can be used across typical optical power meters.’
It’s good to talk
The optical wavelength splitter (OWS), said Tyrk ‘takes in the of wavelengths coming through the network fibre and then takes just some of them out, to connect back to the optical power meters, and then measure separate wavelengths without the need for an expensive DWDM power meter.’
With the market changing and experiencing new challenges almost daily, it is important to keep in contact with the engineers on the front line who will be using this equipment every day. Tyrk said: ‘How do you know what’s needed in the market? The most important thing that we can do is to talk to people and try to adjust to promote certain items more than others. We try to change and introduce new products
constantly, such as the new OWS.’
Similarly to the OWS, the company has looked at another way to make lives easier for engineers. ‘We always try to see what is important and adjust to it,’ said Tyrk.
‘Recently, we amended our range of optical power meters for this reason. There was always a choice between meters for different wavelengths and we have scrapped most of them and developed new power meters that work with most of the wavelengths. So, instead of taking lots of different meters onto site, there is one that will do the same work.’
Tyrk concluded by offering a word of advice to on-site engineers: ‘Always call your vendor and have a chat about what you are looking for. That way you can get, not only the right tool, but also the safe supply of tools.’